Best Practices for Preparing Rough Surfaces
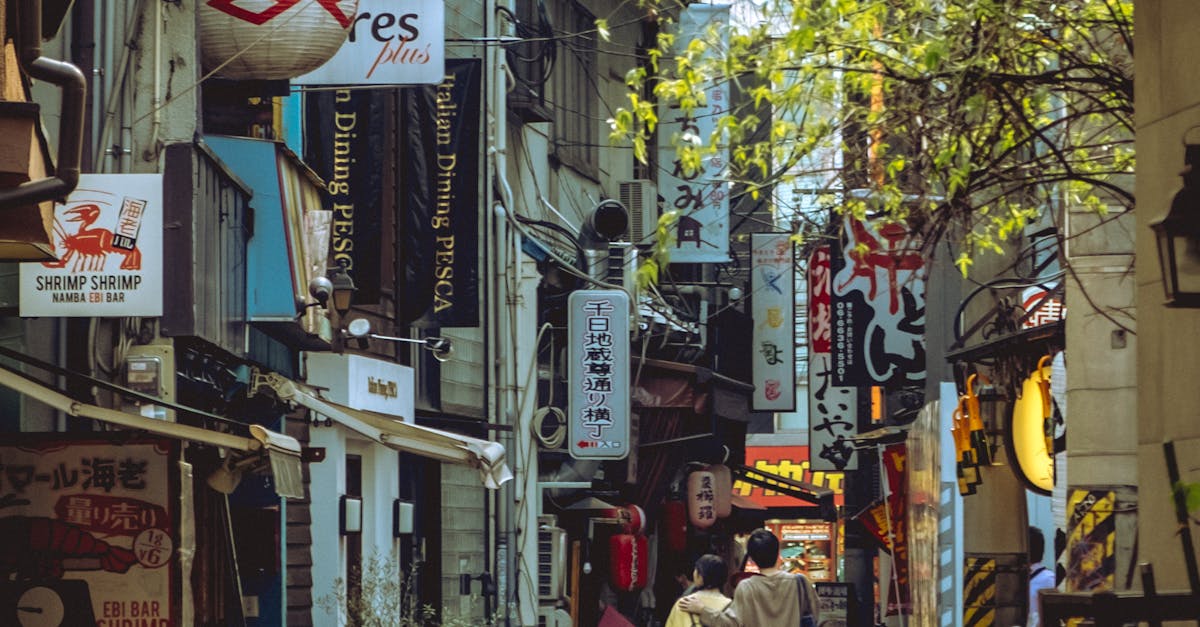
Table Of Contents
Safety Precautions
Ensuring safety during surface preparation is critical. A thorough assessment of the workspace helps identify potential hazards such as sharp edges, dust creation, or chemical exposure. Adequate ventilation is essential when working with materials that produce fumes, and it’s important to keep the area organised to prevent accidents.
Using the right Personal Protective Equipment (PPE) can mitigate risks significantly. Protective eyewear shields against flying debris, while gloves provide a barrier against skin irritants. Respirators may be necessary when sanding or grinding, particularly with materials that generate harmful particles. Sturdy footwear protects against heavy falling objects or sharp tools scattered around the site.
Personal Protective Equipment (PPE) Guidelines
Ensuring proper personal protective equipment (PPE) is essential for anyone working with rough surfaces. Protective eyewear should be worn to guard against dust and debris. Respirators can provide protection from harmful particles and vapours. Gloves suitable for the specific materials being handled are necessary to prevent cuts and skin irritations. Additionally, sturdy footwear should be considered to safeguard feet from heavy objects or sharp equipment.
It's vital to assess the specific hazards present in each workspace before beginning any task. Wearing long-sleeved clothing can help protect against abrasions. Hearing protection might be required when using loud machinery, while hard hats should be used in environments where falling objects are a risk. Careful selection and use of PPE contribute to a safer working environment and help to prevent injuries.
Applying Surface Treatments
Surface treatments play a crucial role in ensuring the durability and performance of various materials. Before applying any treatment, it's essential to prepare the surface adequately. This includes cleaning, degreasing, and ensuring that the surface is free from any contaminants that may interfere with adhesion. Different surfaces may require specific treatments, so it’s important to choose the appropriate product based on the material type and desired outcome.
When applying treatments such as adhesives or sealants, following manufacturer instructions is vital for optimum results. Factors such as temperature, humidity, and surface texture can significantly impact the effectiveness of the treatment. Ensuring proper application techniques, like uniform pressure and coverage, can prevent issues like bubbling or uneven adhesion. Allowing sufficient curing time before further handling or applying additional coatings enhances the longevity and performance of the treatment.
Best Practices for Adhesives and Sealants
When selecting adhesives and sealants for rough surface applications, it is essential to choose products that are specifically formulated for the intended materials. A proper bond relies on compatibility, so carefully inspect the manufacturer's specifications. Ensure surfaces are clean, free from dust, oils, or contaminants before applying the adhesive. Minor imperfections in rough areas may be effectively filled with the chosen material, enhancing adhesion and durability.
Applying adhesives and sealants demands attention to detail for optimal performance. Follow the manufacturer's instructions regarding application methods, including recommended temperatures and curing times. Use tools that facilitate even distribution and avoid excessive application that could lead to overflow or messiness. For maximum effectiveness, consider environmental factors such as humidity and temperature, as they can affect drying and curing times. Proper storage of unused products is also important; ensure they are kept in a cool, dry place to maintain their efficacy.
Techniques for Smoothing Rough Areas
Smoothing rough surfaces involves various techniques that cater to the specific material and the desired finish. Utilizing sanding is a common method for wood and some metals. Sandpaper comes in different grits, and starting with a coarser grit helps remove larger imperfections. Gradual progression to finer grits ensures a smooth finish. Equally, for surfaces that are too tough for sanding, grinding can be effective. Angle grinders provide a powerful alternative for smoothing concrete or masonry.
Another popular technique involves using a combination of scraping and filling. Scrapers allow for precise removal of excess material or rough edges, particularly in woodworking. After achieving a smoother surface, filling gaps or holes with appropriate fillers can create an even finish. Once the filler has dried, sanding it down helps blend it seamlessly with the surrounding area. This layered approach not only rectifies rough spots but enhances overall aesthetics and durability.
Effective Sanding and Grinding Methods
Sanding is a fundamental method for achieving a smooth finish on rough surfaces. Selecting the appropriate grit is crucial; starting with a coarser grit, such as 60-80, helps to remove larger imperfections and transitions seamlessly to finer grits, typically between 120-220, which refine the surface. Maintaining consistency and even pressure across the area is essential to avoid uneven spots. Always work in the direction of the grain when dealing with wood to prevent scratches from becoming too pronounced.
Grinding serves a different purpose, often used for metal and masonry surfaces. It requires a different set of tools, such as angle grinders or bench grinders, which can effectively remove more material. Using the right wheel or disc for the material at hand is vital, as different surfaces necessitate various grinding parameters. The speed and technique employed significantly influence the final result; maintaining a steady movement often leads to a more uniform surface. Regularly checking your progress during grinding can help prevent gouging and keep the work area manageable.
FAQS
What safety precautions should I take when preparing rough surfaces?
Always ensure you wear appropriate personal protective equipment (PPE) such as safety goggles, gloves, and a dust mask. Additionally, make sure the work area is well-ventilated and clear of any hazards.
What type of personal protective equipment (PPE) is recommended for this task?
Recommended PPE includes safety goggles to protect your eyes, gloves to prevent skin irritation, a dust mask to avoid inhaling particles, and hearing protection if using loud power tools.
What are the best practices for applying adhesives and sealants on rough surfaces?
Ensure the surface is clean and dry before application. Use the recommended amount of adhesive or sealant, apply evenly, and allow adequate curing time as per manufacturer instructions for optimal results.
What techniques can I use to effectively smooth rough areas?
Effective techniques include sanding with the appropriate grit sandpaper, using a grinder for more stubborn areas, or employing a power sander for larger surfaces to achieve a smoother finish.
Are there specific methods for sanding and grinding that are more effective?
Yes, using progressively finer sandpaper will help achieve a smoother surface. When grinding, use a steady, even motion and avoid applying too much pressure to prevent damage to the surface.
Related Links
Environmental Considerations in Sign Surface PreparationPreparing Metal Surfaces for Sign Applications
Surface Preparation: Tips for Adhesion and Longevity
The Role of Surface Preparation in Sign Durability
Step-by-Step Guide to Surface Preparation for Signage